Learner Zone
Motor Vehicle HubEngine Performance
The engine is the heart of your car. It is a complex machine that converts heat from burning gas into the force that turns the wheels and moves the vehicle.
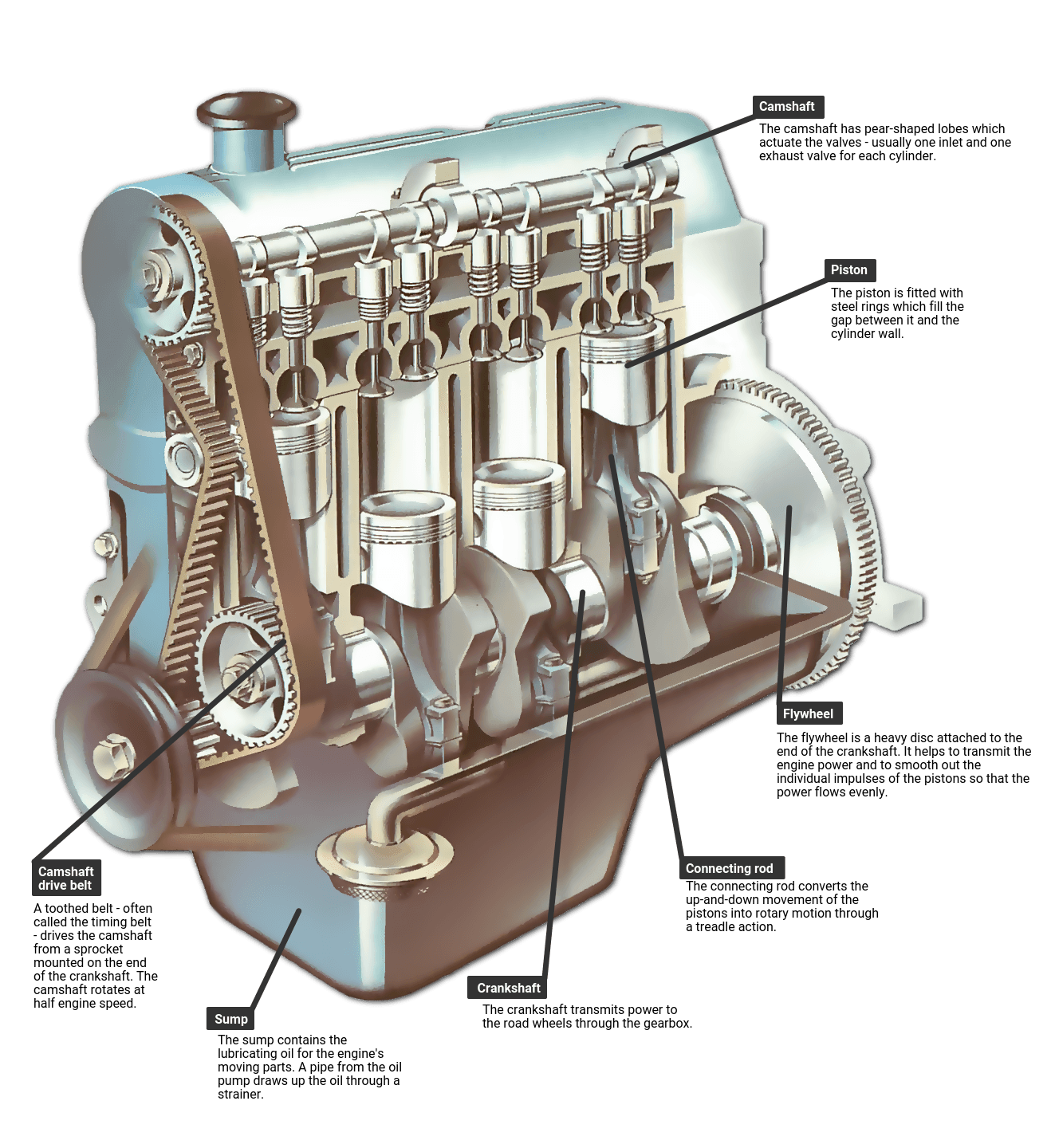
carburetor
The conversion of fuel energy into power in an engine starts when petrol is mixed with air in a device called a carburetor to form a highly combustible mixture.
The mixture is drawn into the cylinders through valves and compressed by a piston. It is then ignited by a spark plug. Rapid expansion of the burning gas (combustion) drives the piston down the cylinder. The downward thrust is changed by the connecting rod to rotary movement of the crankshaft in much the same way as a cyclist pressing the pedal turns the chain wheel.
The downward stroke of the piston is known as the power stroke in a four-stroke cycle. It occurs once in every four strokes of the piston’s movement.
The cycle starts with the induction stroke. With the exhaust valve closed, a downward movement of the piston sucks fuel from the carburetor into the cylinder. The mixture enters through the inlet valve, which has been opened by the camshaft. The following upward movement of the piston is the compression stroke. The exhaust valve remains closed and the inlet valve also closes, so the mixture in the cylinder is compressed by the rising piston into the combustion chamber.
A spark from the spark plug ignites the mixture and causes it to expand rapidly, driving the piston down in a power stroke. As the piston rises once more, the inlet valve remains closed but the exhaust valve opens. This allows waste products to escape through the exhaust, and is called the exhaust stroke.
The camshaft continues to rotate, the exhaust valve closes and the inlet valve opens and the four-stroke cycle starts again.
Watch this short video to know more about how carburetors work.
fuel injectors
For an engine to run efficiently it needs to be supplied the right quantity of fuel and air. Traditionally this is controlled by the carburetor, however many cars now use fuel-injected engines where the fuel is delivered in precise bursts. These kinds of engines are more efficient, more powerful, and more economical.
The fuel injection system in petrol engines is always indirect, with petrol injected into the inlet manifold or inlet port rather than directly into the combustion chambers. This ensures that the fuel is well mixed with the air before it enters the chamber.
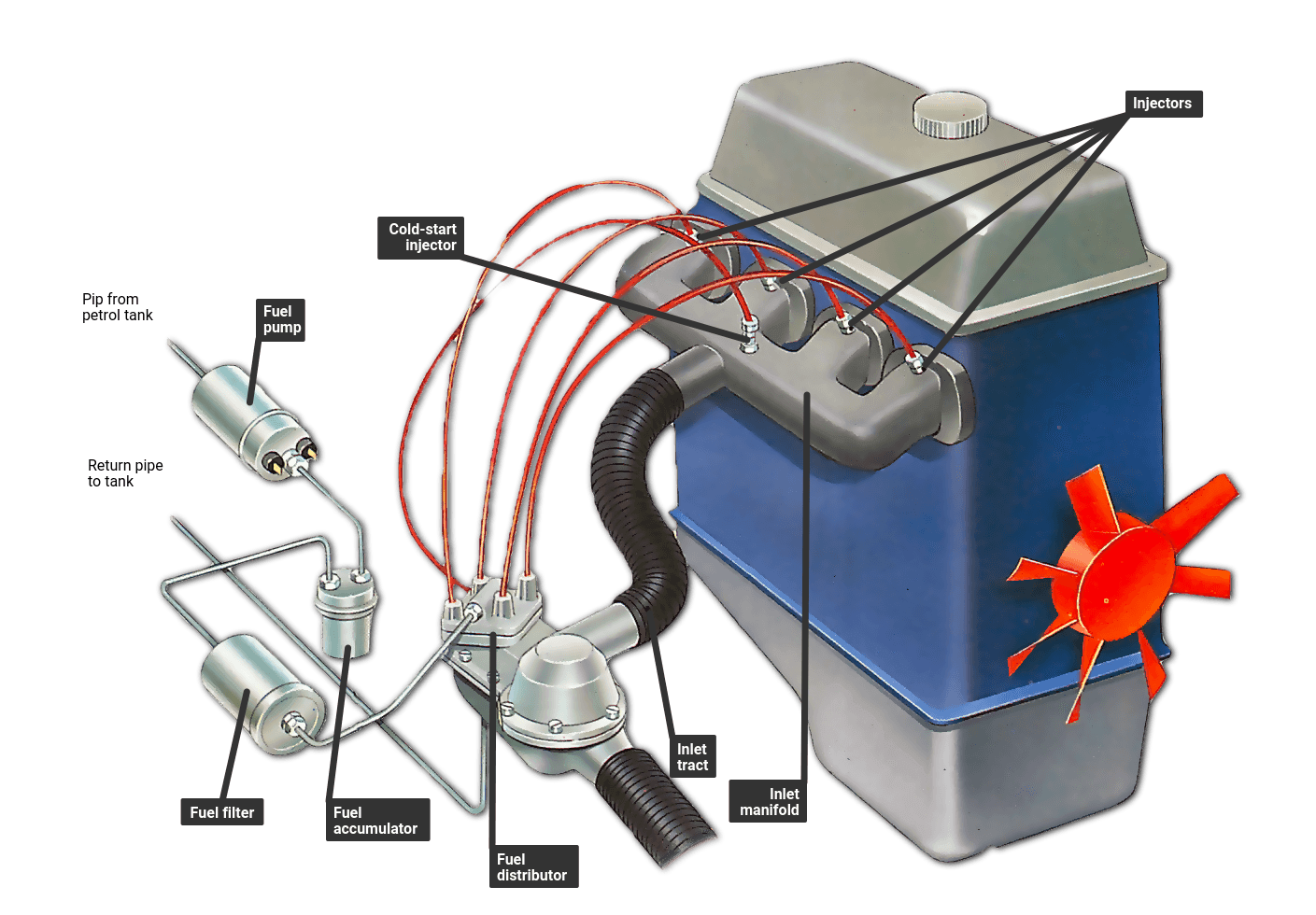
Many diesel engines use indirect injection in which the diesel fuel is injected into the pre-combustion chamber which connects it to the cylinder head. Only air is drawn into the cylinder. It is heated so much by compression that atomized fuel injected at the end of the compression stroke self-ignites.
All modern petrol systems use indirect injection. A special pump sends the fuel under pressure from the fuel tank to the engine bay where it is distributed individually to each cylinder. Depending on the system, the fuel is fired into either the inlet manifold or the inlet port via an injector. The fuel mixes with the air passing through the inlet manifold and the mixture enters the combustion chamber.
Watch these videos to learn more about diesel fuel systems and electronic fuel injection.
The injectors through which the fuel is sprayed are screwed into either the inlet manifold or the cylinder head. Fuel is fired towards the inlet valve.
The injectors are one of two types, depending on the injection system. The first system uses continuous injection to spray fuel into the inlet port all while the engine is running. The injector acts as a spray nozzle to break up the fuel into a fine mist. It does not control the fuel flow. The amount of fuel sprayed is increased or decreased by a mechanical or electrical control unit. The other system is timed injection where the fuel is delivered in bursts to coincide with the induction stroke of the cylinder. As with continuous injection, timed injection can be controlled mechanically or electronically.
The earliest systems were mechanically controlled. They are often called petrol injection and the fuel flow is controlled by a mechanical regulator assembly. Such systems have now been largely superseded by electronic fuel injection.
emissions
In automobiles, emission control means to limit the discharge of noxious gases produced.
The main sources that produce these gases: are the exhaust, the crankcase, the fuel tank and carburetor. The exhaust pipe discharges hydrocarbons, carbon monoxide, oxides of nitrogen and sulfur and traces of various acids, alcohols, and phenols. The crankcase is a lesser source of unburned hydrocarbons and carbon monoxide. In the fuel tank and the carburetor, hydrocarbons that are continually evaporating from petrol contribute to pollution. A variety of systems for controlling emissions from all these sources have been developed.
In the crankcase leaked combustion gases are combined with ventilating air and returned to the intake manifold for reburning in the combustion chamber. The device that performs this function is known as the positive crankcase ventilation valve, or PCV valve.
In the exhaust, two types of systems are used: the air injection system and the exhaust gas recirculation (EGR) system. In EGR a portion of exhaust gases are directed back to the cylinder head, where they are combined with the fuel/air mixture and enter the combustion chamber. The recirculated exhaust gases lower the temperature of combustion, a condition that favours lower production of nitrogen oxides. In a typical air injection system, an engine-driven pump injects air into the exhaust manifold, where the air combines with unburned hydrocarbons and carbon monoxide at a high temperature to continue the combustion process. In this way a large percentage of the pollutants that were formerly discharged through the exhaust are burned.
Another area for additional combustion is the catalytic converter. As the exhaust gases are passed through the packed beads, the metals act as catalysts to induce the hydrocarbons, carbon monoxide, and nitrogen oxides in the exhaust to convert to water vapour, carbon dioxide, and nitrogen.
In the past, fumes evaporating from the fuel tank and carburettor were vented directly into the atmosphere. Today those emissions are greatly reduced by sealed fuel tank caps and the evaporative control system, the heart of which is a canister of activated charcoal capable of holding up to 35% of its own weight in fuel vapour. The vapours flow from the sealed fuel tank to a vapour separator, which returns raw fuel to the tank and channels vapour through a purge valve to the canister. The canister acts as a storehouse; when the engine is running, the vapours are drawn by the vacuum from the canister through a filter and into the combustion chamber, where they are burned.
Watch these videos to learn more about exhausts and emission control systems.